The Evolution of the Automotive Industry: A Deep Dive into **Automotive Plastic Molding**
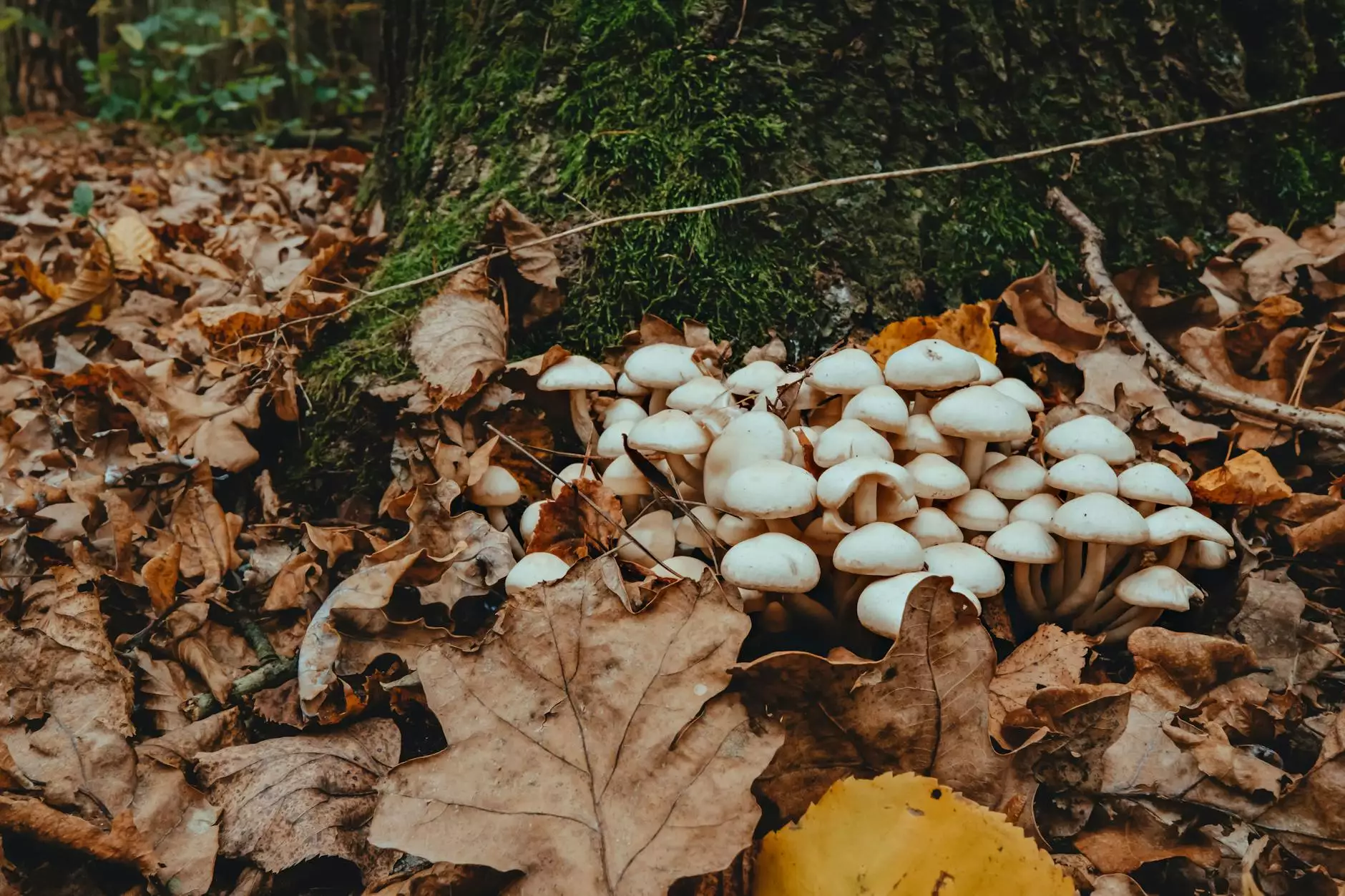
The automotive industry has undergone significant transformations over the decades, with automotive plastic molding emerging as a critical technology. This process not only enhances vehicle aesthetics but also improves overall functionality and performance. In this article, we will explore the intricate world of automotive plastic molding, its processes, applications, and the transformative benefits it brings to modern automobiles.
What is Automotive Plastic Molding?
Automotive plastic molding refers to the manufacturing techniques used to shape and design plastic parts for vehicles. This process involves the use of heat and pressure to form plastic into specific shapes, which are then used for various components in automobiles. It is a versatile method that offers manufacturers the ability to produce custom designs and maintain lightweight vehicle structures, which is paramount in today's automotive advancements.
The Benefits of Automotive Plastic Molding
Understanding the benefits of automotive plastic molding is essential for manufacturers, designers, and even consumers. Here are some of the most significant advantages:
- Weight Reduction: Plastic parts significantly reduce the weight of vehicles, leading to improved fuel efficiency and reduced emissions.
- Cost-Effectiveness: Molding processes are often less expensive than traditional metal fabricating methods, allowing for lower production costs.
- Design Flexibility: Plastics can be molded into complex shapes and sizes, providing designers abundant creative freedom.
- Corrosion Resistance: Unlike metals, plastics do not rust, which enhances the longevity of components.
- Insulation Properties: Plastics offer better thermal and acoustic insulation compared to metal parts.
Key Processes in Automotive Plastic Molding
There are several key processes involved in the automotive plastic molding industry. Understanding these processes helps in grasping how various vehicle components are manufactured:
1. Injection Molding
Injection molding is the most common method used in automotive plastic molding. In this process, plastic material is melted and injected into a mold where it cools and solidifies into the desired shape. This method is ideal for producing large quantities of identical parts with high precision.
2. Blow Molding
Blow molding is used primarily for hollow plastic parts such as fuel tanks. The process involves inflating heated plastic into a mold to form the desired shape. This technique is especially useful for producing large volumes of consistent products.
3. Compression Molding
Compression molding involves placing plastic material in a heated mold and then applying pressure. This method is particularly useful for thermosetting plastics and is often used in the production of automotive interior components.
4. Rotational Molding
Rotational molding is a process usually reserved for larger, hollow parts. The mold is rotated on multiple axes, allowing the plastic to coat the interior surfaces evenly, resulting in uniformly thick structures.
Applications of Automotive Plastic Molding
Automotive plastic molding is utilized in various applications across a vehicle's design and engineering aspects:
- Exterior Panels: Lightweight bumper covers, body panels, and trim pieces that improve fuel efficiency.
- Interior Components: Dashboard assemblies, door panels, and center consoles that enhance both aesthetics and functionality.
- Under-the-Hood Parts: Engine covers, air intake ducts, and housings that offer weight savings without compromising performance.
- Lighting Systems: Lenses and housing for headlights, taillights, and signal lights that utilize precise molding for optimal performance.
- Sealing and Gaskets: Gaskets made from molded plastic provide effective sealing solutions that contribute to overall vehicle efficiency.
Sustainability in Automotive Plastic Molding
As the automotive industry faces increasing pressure to adopt sustainable practices, automotive plastic molding plays a pivotal role in manufacturing eco-friendly products. Here are some ways in which this process contributes to sustainability:
- Recyclability: Many plastics used in automotive applications are recyclable, meaning end-of-life parts can be reprocessed and reused, reducing waste.
- Reduced Energy Consumption: Lightweight plastic parts contribute to greater fuel efficiency, which lowers greenhouse gas emissions throughout a vehicle's lifecycle.
- Alternative Materials: Ongoing research is leading to the development of bio-based and biodegradable plastics, pushing the industry towards increasingly sustainable practices.
The Future of Automotive Plastic Molding
Looking ahead, the future of automotive plastic molding promises significant advancements driven by technology and innovation. Here are some trends that are shaping the landscape:
1. Advanced Manufacturing Techniques
Techniques such as additive manufacturing and 3D printing are being integrated into traditional molding processes to enhance design flexibility and speed up prototyping.
2. Smart Plastics
Enhancements in material science are leading to the creation of 'smart plastics,' which can react to environmental stimuli, improving the functionality of automotive components.
3. Integration with Electric Vehicles (EVs)
The growing demand for EVs presents unique challenges that automotive plastic molding can address, particularly regarding weight reduction and battery housing solutions.
4. Digitalization
Industry 4.0 is driving the digital transformation of automotive plastic molding, enabling predictive maintenance, better supply chain management, and enhanced quality control through data analytics.
Partnering with Experts in Automotive Plastic Molding
At deepmould.net, we specialize in delivering top-notch automotive plastic molding solutions tailored to your needs. Our team of experts utilizes cutting-edge technology and innovative approaches to ensure your products meet the highest standards of quality and efficiency.
If you're looking to enhance your automotive components through reliable plastic molding solutions, do not hesitate to contact us today. Together, we can shape the future of the automotive industry.
Conclusion
In conclusion, automotive plastic molding is a vital process within the automotive industry that offers numerous advantages, including weight reduction, cost-effectiveness, and design flexibility. As the industry continues to evolve, the integration of sustainable practices and advanced technologies will be crucial. By embracing these innovations, manufacturers can ensure they are not only meeting current demands but are also paving the way for a more sustainable and efficient future.
Stay tuned to our blog for more insights into the world of automotive plastic molding and the exciting developments within the automotive sector.