Unlocking the Potential of Plastic Injection Molding in Business
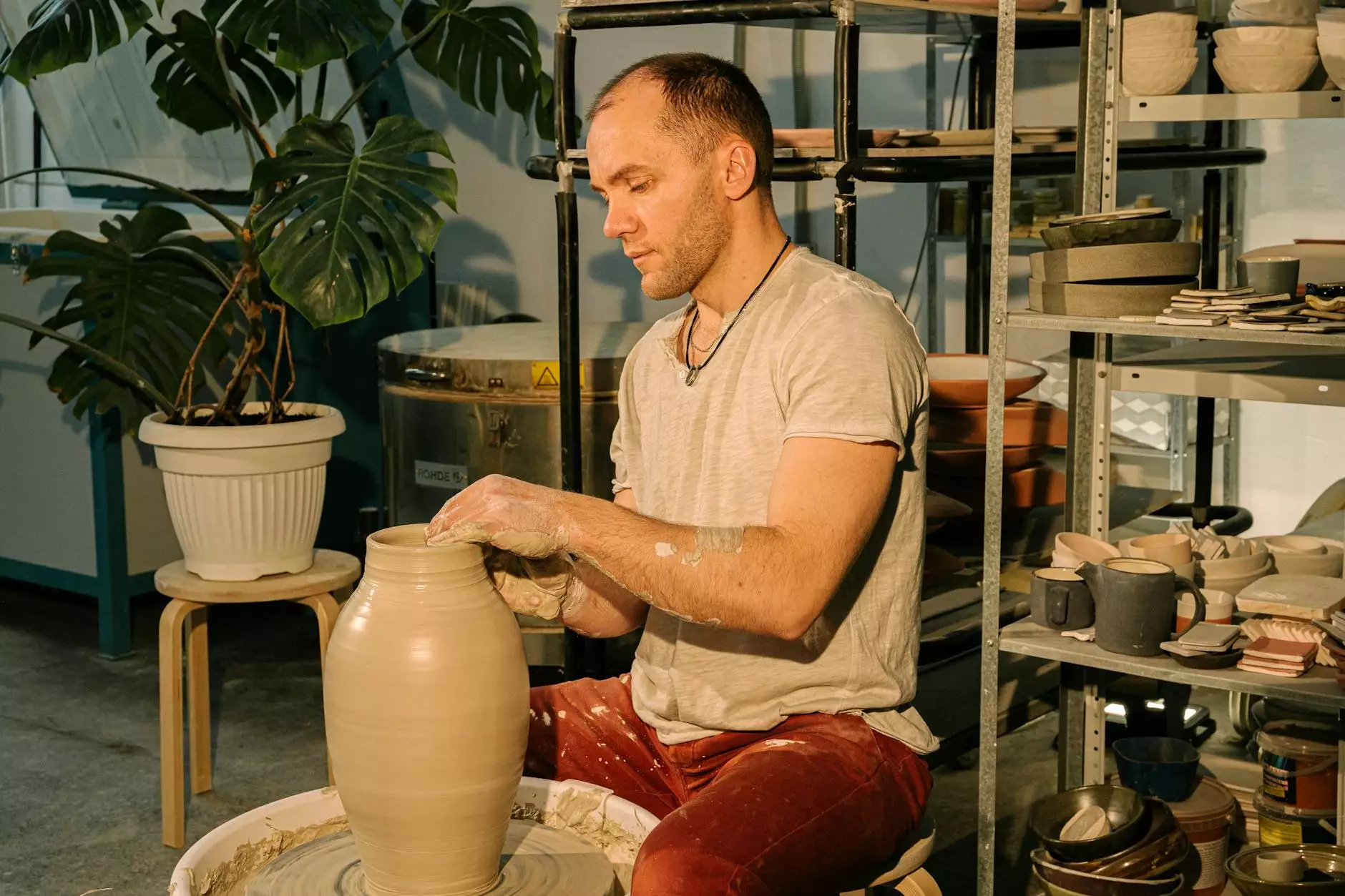
Plastic injection molding is a transformative manufacturing process that enables businesses to create complex and customizable plastic components with precision and efficiency. This article will delve into the depths of plastic injection molding, its applications, benefits, and its critical role in the success of modern businesses, particularly in the realm of metal fabricators.
What is Plastic Injection Molding?
Plastic injection molding is a manufacturing process where molten plastic material is injected into a mold to produce specified parts. This technique is popular due to its ability to produce high volumes of identical components with exceptional accuracy. The process typically involves the following steps:
- Material Selection: Various types of plastic (such as thermoplastics and thermosets) are chosen based on the desired characteristics of the final product.
- Injection: The chosen plastic material is heated until it becomes molten and is then injected into a custom-made mold.
- Cooling: Once the mold is filled, the material cools and solidifies, taking the shape of the mold.
- Ejection: The finished part is ejected from the mold, ready for further finishing processes if necessary.
Advantages of Plastic Injection Molding
The popularity of plastic injection molding can be attributed to several key advantages:
Cost-Effectiveness
One of the most significant benefits is the cost-effectiveness of the process. Once the mold is created, the cost per unit decreases dramatically, making it ideal for mass production.
High Efficiency
This method allows for the rapid production of large quantities of parts, which can lead to significant time savings in the production line.
Design Flexibility
Plastic injection molding enables the creation of complex shapes and designs that would be impossible or very costly to achieve with other manufacturing methods.
Enhanced Product Quality
The process provides a high level of precision and repeatability, resulting in excellent surface finishes and tight tolerances for parts.
Various Applications of Plastic Injection Molding
The applications of plastic injection molding are vast and span across numerous industries, including:
Automotive Industry
In the automotive sector, components such as dashboard assemblies, body panels, and interior trim are commonly produced using plastic injection molding.
Consumer Goods
From kitchen utensils to electronic housings, consumer products significantly benefit from the efficiency and adaptability of injection molded plastic.
Medical Devices
Medical equipment and devices require stringent quality and precision standards that plastic injection molding meets through its reliable manufacturing process.
Packaging
Plastic injection molding plays a crucial role in producing packaging components like bottles, containers, and lids, ensuring product integrity and safety.
The Importance of Quality in Plastic Injection Molding
Ensuring high quality in plastic injection molding is paramount, as it directly affects the performance and durability of the final product. Businesses like DeepMould.net understand the importance of utilizing the latest technology and quality control processes to maintain high standards. Key quality considerations include:
- Material Quality: Using high-quality raw materials is essential to achieving the desired properties in the final product.
- Mold Design: Well-designed molds ensure accurate and efficient production while minimizing defects.
- Process Control: Rigorous monitoring of the injection molding process helps in identifying potential issues before they affect production quality.
Challenges in Plastic Injection Molding
While plastic injection molding presents numerous benefits, businesses must also navigate several challenges:
Initial Setup Costs
The initial cost of mold creation can be substantial, which might deter small businesses from utilizing this method. However, the long-term savings from mass production often outweigh this initial investment.
Complexity in Mold Design
Creating molds for complex designs requires expertise and can be time-consuming. It's crucial for businesses to collaborate with experienced mold makers to ensure the design process is smooth.
Material Limitations
Not all plastics are suitable for injection molding. Understanding the properties of different materials is vital to selecting the right one for a given application.