Enhancing Manufacturing Efficiency: The Role of CNC Machining Parts Factory
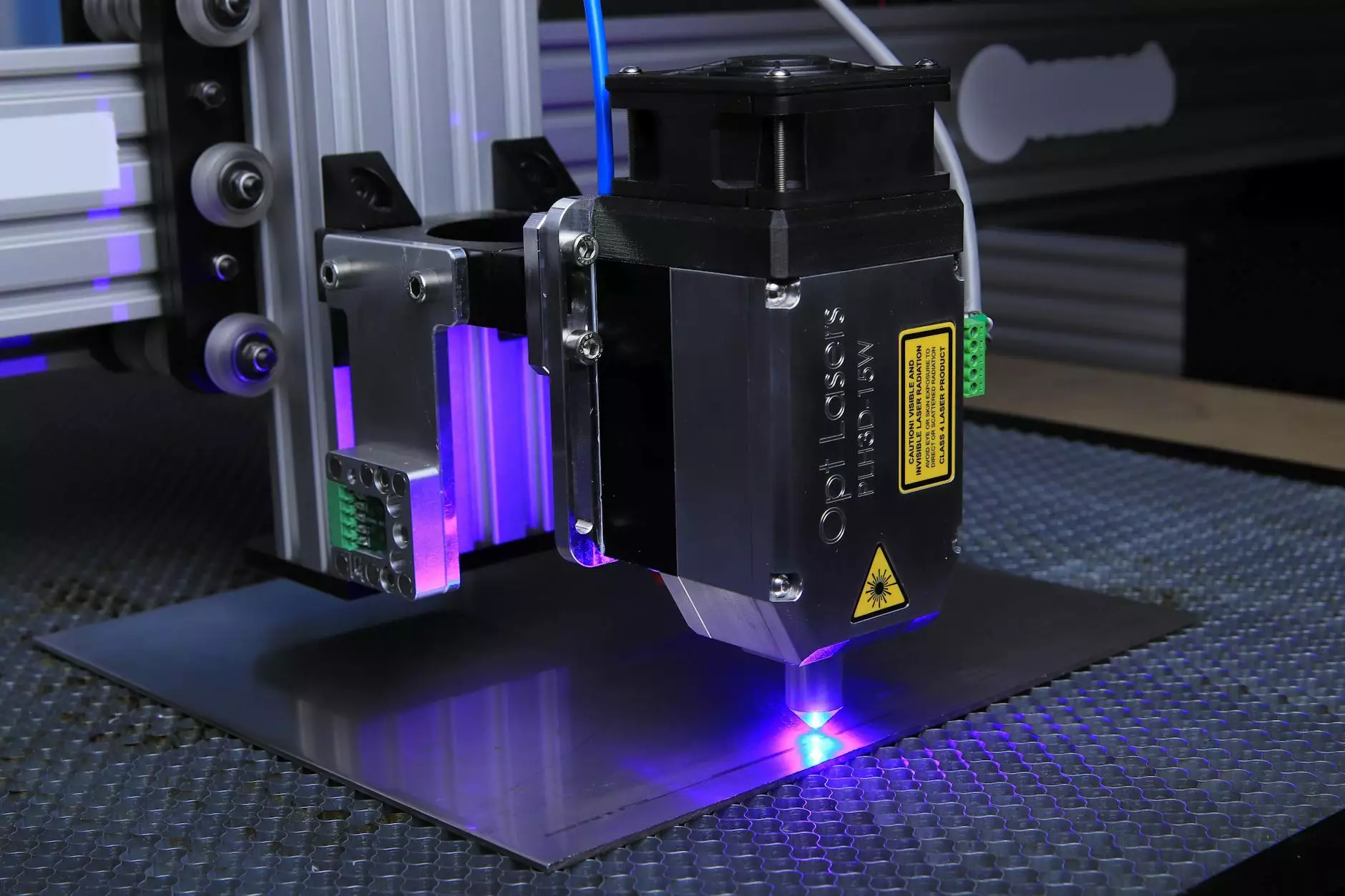
In today’s highly competitive manufacturing landscape, precision and efficiency are key components for success. Companies looking to enhance their production capabilities are increasingly turning to cnc machining parts factories for their ability to produce high-quality parts with remarkable accuracy and consistency. This article delves into the significance of CNC machining factories, their operational advantages, and how they can redefine your business's manufacturing process.
Understanding CNC Machining: The Basics
CNC machining, or Computer Numerical Control machining, represents a breakthrough in manufacturing technology. This process involves the use of computers to control machine tools, which allows for the meticulous removal of material from a workpiece to create complex shapes and components. Here’s a closer look at the fundamental aspects of CNC machining:
- Automation: CNC machines operate autonomously, utilizing programming code to execute precise movements that produce intricate designs.
- Versatility: CNC machining can work with a wide range of materials, including metals, plastics, and composites, making it ideal for diverse industries.
- Scalability: From prototyping to full-scale production, CNC machining services can be tailored to meet the demands of any project size.
The Advantages of Partnering with a CNC Machining Parts Factory
Choosing the right manufacturing partner can have profound implications for your business. Here are some of the standout benefits of collaborating with a cnc machining parts factory:
1. Enhanced Quality and Precision
One of the chief advantages of CNC machining lies in its ability to deliver unparalleled precision. With tolerances as tight as ±0.001 inches, CNC processes ensure that every part produced meets your specifications, reducing the risk of defects and costly rework.
2. Cost-Effectiveness
While the initial investment in CNC technology can be significant, the long-term savings are considerable. By streamlining production processes and minimizing waste, CNC machining significantly cuts down overall manufacturing costs.
3. Increased Efficiency and Speed
CNC machining allows for rapid production schedules. Once a design is programmed, machines can operate continuously, producing large volumes of high-quality components in a fraction of the time traditional methods require.
4. Customization Capabilities
Modern CNC machining technology supports complex customizations, enabling manufacturers to create bespoke parts tailored to specific project needs. This adaptability is crucial for companies that require unique designs or small production runs.
5. Improved Safety
Automation significantly enhances workplace safety. By minimizing human interaction with dangerous machinery, CNC machining reduces the likelihood of workplace accidents, fostering a safer environment for workers.
Industries Benefiting from CNC Machining Parts
The versatility of cnc machining parts factories ensures that a multitude of industries reap the benefits of this technology. Here are some key sectors that have transformed their manufacturing processes through CNC machining:
Aerospace
Aerospace manufacturers demand the highest levels of precision. CNC machining allows for the production of lightweight, high-strength components that meet stringent industry standards.
Automotive
The automotive industry utilizes CNC machining to produce a variety of parts, from engine components to intricate interior fixtures. The consistency and reliability of CNC processes are essential to maintaining quality in this high-volume sector.
Medical Devices
With the need for exact specifications in medical devices, CNC machining plays a critical role in manufacturing parts that adhere to rigorous health and safety regulations.
Electronics
Electronics manufacturing benefits from CNC machining’s precision in producing components like housings and heatsinks, which are integral to the performance of electronic devices.
Consumer Goods
From small appliances to furniture, CNC machining allows for the rapid production of high-quality consumer goods, ensuring that manufacturers can keep up with market demand.
Choosing the Right CNC Machining Parts Factory
Selecting a reliable cnc machining parts factory can be a daunting task. Here are essential factors to consider when making this crucial choice:
1. Experience and Expertise
Look for a factory with extensive experience in the CNC machining industry. Their expertise will translate into better advice, improved processes, and superior product quality.
2. Technology and Equipment
Ensure that the factory employs the latest CNC technology, which guarantees precision and efficiency. Advanced machines can handle a broader range of materials and part complexities.
3. Quality Control Measures
A strong quality assurance program is vital. Choose a factory that implements stringent quality control checks at every production stage to ensure that parts meet exact specifications.
4. Customer Service
Excellent customer service is crucial for successful partnerships. Reliable communication and support can enhance collaboration and resolve any issues that arise promptly.
5. Flexibility and Scalability
Your chosen factory should be capable of scaling production up or down according to your specific needs, allowing for a flexible approach that can adapt to market fluctuations.
Future Trends in CNC Machining
The world of CNC machining is evolving rapidly. Stay ahead by understanding the key trends shaping the future of machining technology.
1. Industry 4.0 and Smart Factories
The introduction of Industry 4.0 is revolutionizing manufacturing through the integration of IoT (Internet of Things) technologies. Smart factories will enable real-time monitoring and optimization of production processes.
2. Advanced Materials
The development of advanced materials such as carbon fiber and titanium alloys is enhancing the capabilities of CNC machining, allowing for the production of lighter and stronger components than ever before.
3. Additive Manufacturing Integration
As additive manufacturing (3D printing) becomes more prevalent, the integration of CNC machining and 3D printing processes will create innovative solutions for producing complex parts.
4. Sustainability Practices
As environmental concerns grow, CNC machining factories are adopting sustainable practices by reducing waste, optimizing energy usage, and implementing recycling programs.
Conclusion: The Future of Manufacturing with CNC Machining
In conclusion, the role of a cnc machining parts factory is pivotal in shaping the future of manufacturing. By leveraging the advantages of CNC technology, businesses can achieve greater efficiency, accuracy, and flexibility in their production processes. As industries continue to evolve, embracing CNC machining will be essential for companies aiming to remain competitive in the landscape of modern manufacturing. Partnering with a trusted CNC machining factory like DeepMould can lead to transformative results, setting your business on a path to unprecedented growth and success.