Exploring the World of Injection Factories: A Comprehensive Guide
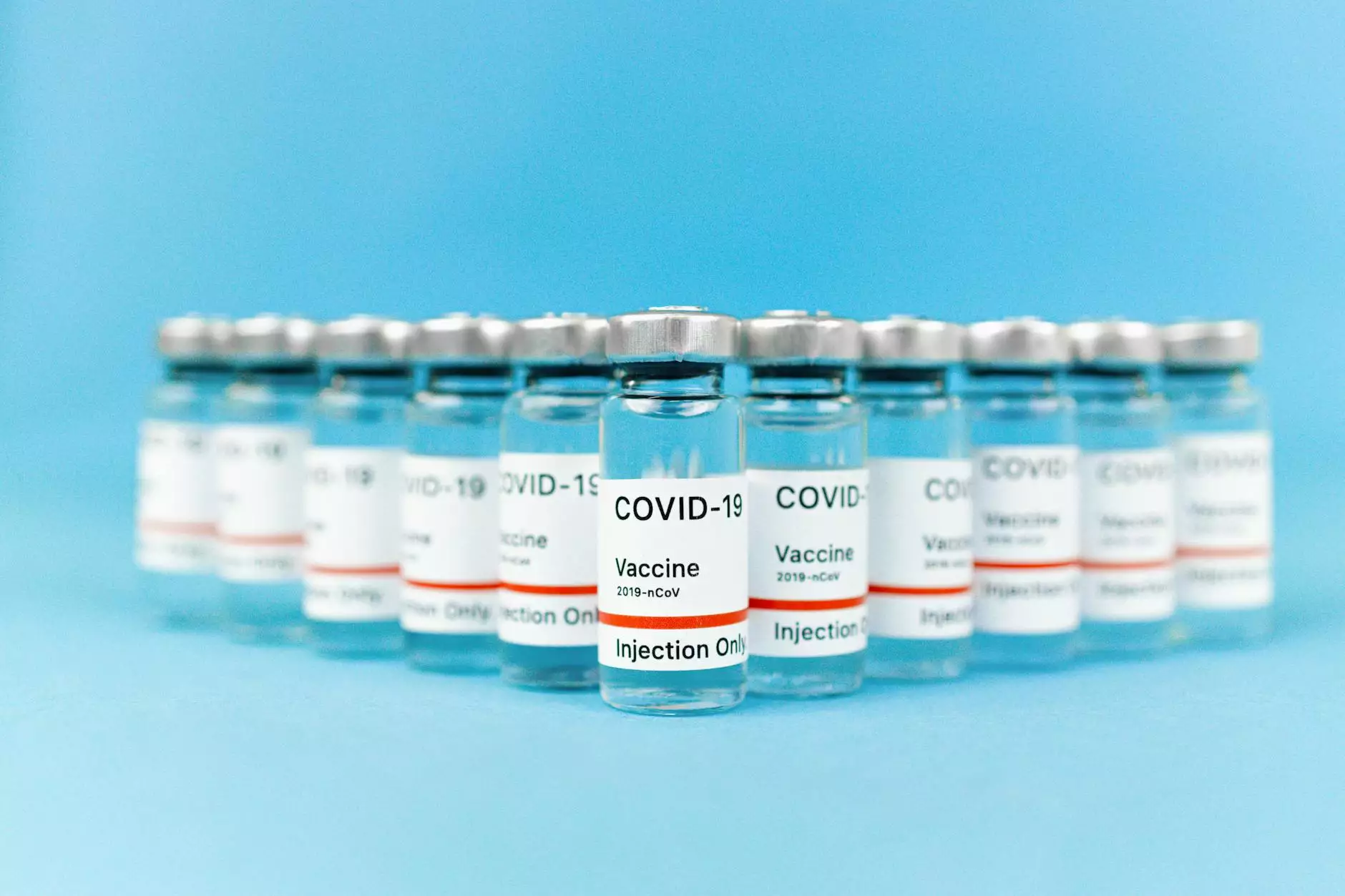
In the realm of manufacturing, injection factories are frequently at the forefront of innovation. As we delve into the intricate details of these facilities, we will examine their impact on various industries, particularly in the fields of art supplies, product design, and 3D printing. This article aims to provide a thorough understanding of injection molding processes, their applications, and the future landscape of manufacturing technology.
What is an Injection Factory?
An injection factory is a specialized manufacturing facility designed to produce parts and products through the injection molding process. This method involves injecting molten material, typically plastic, into a mold, allowing it to cool and solidify into the desired shape. The capabilities of injection factories have expanded considerably, accommodating various materials, including polymers, metals, and composites.
The Injection Molding Process: A Step-by-Step Overview
Understanding the injection molding process is crucial for anyone involved in manufacturing, whether in art supplies or product design. Below are the key steps in the injection molding cycle:
- Material Preparation: Raw plastic or other materials are processed into small pellets which are ready for melting.
- Injection: The pellets are heated until they melt and are then injected into the mold at high pressure.
- Cooling: The molten material is allowed to cool, solidifying in the shape of the mold.
- Demolding: Once cooled, the mold opens, and the newly formed product is ejected.
- Finishing: The product may require additional processing such as trimming, painting, or assembly.
The Significance of Injection Factories in Modern Manufacturing
The role of injection factories transcends traditional manufacturing capabilities. They are pivotal in creating products that are not only functional but aesthetically appealing. This is particularly important in sectors such as art supplies and product design, where quality and precision are paramount.
Benefits of Using Injection Molding in Art Supplies
The intersection of injection factories and the art supplies industry is vibrant with innovation. This manufacturing method offers numerous advantages:
- Consistency: Injection molding produces uniform products, which is essential for artists seeking reliable materials.
- Complex Shapes: The process allows for intricate designs, enabling the creation of innovative tools and products.
- Material Efficiency: Minimal waste is generated during the process, making it environmentally friendly.
- Cost-Effectiveness: Once the mold is created, the production costs significantly decrease, facilitating competitive pricing.
Fostering Creativity: Injection Factories and Product Design
In the domain of product design, collaboration with injection factories opens up new avenues for creativity. Designers can exploit the capabilities of injection molding to bring their visions to life. Here’s how:
Rapid Prototyping
Injection factories enable rapid prototyping, which is crucial for designers. They can create several iterations of a design quickly, test them, and refine their ideas based on real-world feedback.
Customization
One of the standout features of injection molding is the ability to produce customized products at scale. This flexibility allows designers to tailor products to specific client needs or market demands, thereby enhancing customer satisfaction.
3D Printing vs. Injection Molding: A Comparative Analysis
With the advent of 3D printing, many have raised questions about its relevance compared to traditional methods like injection molding. Each technique has its merits, and understanding their differences can aid businesses in making informed decisions.
Speed and Efficiency
While 3D printing is excellent for rapid prototyping, injection molding generally offers faster production times for larger quantities. Injection factories excel in mass production, delivering high volumes with minimal downtime.
Cost Implications
Initial setup costs for injection molding can be higher due to the need for mold creation. However, for large-scale production, the cost per unit diminishes significantly, which can outweigh the benefits of 3D printing for larger runs.
Material Choices
Injection molding supports a wider array of materials, including specific plastics that are difficult to 3D print. This gives injection factories a distinct advantage when durability and material performance are critical.
The Future of Injection Factories: Trends and Innovations
The future of injection factories looks promising, with several trends shaping the landscape of manufacturing:
Smart Manufacturing
With the integration of IoT (Internet of Things), injection factories are becoming smarter. Real-time data analytics enables manufacturers to optimize their processes, reduce waste, and enhance efficiency.
Sustainability Initiatives
As industries worldwide shift toward sustainability, injection factories are adopting eco-friendly practices. This includes using recycled materials, minimizing waste, and reducing the carbon footprint through efficient energy use.
Advancements in Mold Technology
Continuous advancements in mold design are enabling the production of more complex parts, improving production speeds, and reducing maintenance costs.
Conclusion: The Integral Role of Injection Factories
In summary, injection factories play a crucial role in contemporary manufacturing, particularly within the realms of art supplies, product design, and 3D printing. Their ability to produce high-quality, consistent products on a large scale while remaining environmentally and cost-effective cannot be overstated. As technology continues to advance, the potential of injection factories to drive innovation and enhance creativity will only increase, making them vital players in the economic landscape.
For businesses looking to innovate and stay competitive, understanding the strengths and capabilities of injection factories is essential. Embracing these technologies not only leads to enhanced product development but also positions businesses at the forefront of their respective industries.